11月6日,第33届中国新闻奖评选结果揭晓,《工人日报》重大主题报道作品《先进制造业企业究竟先进在哪里》荣获三等奖。该作品由五篇系列报道构成,聚焦五家具有较强创新能力,产品具备较高附加值、技术含量和市场竞争力的先进制造业企业,探寻其转型发展的典型经验。今天,让我们一起回顾品读这个获奖作品↓↓
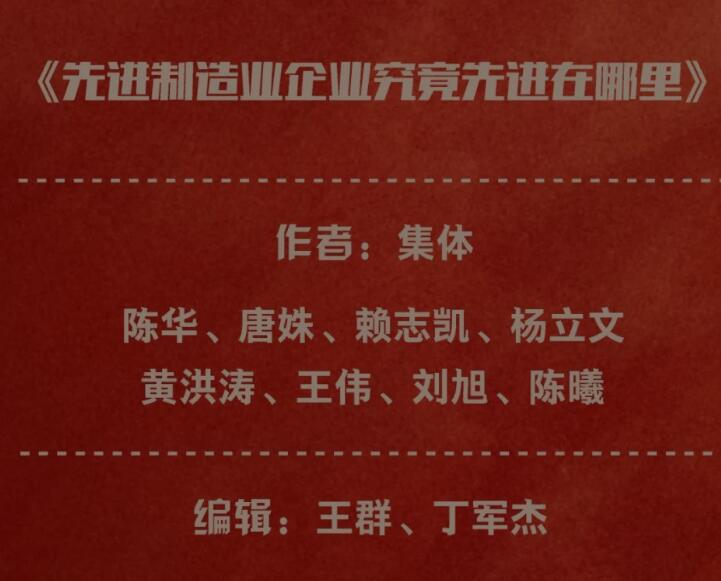
从提供单一产品向提供“产品+服务”乃至“制造融合服务”转变
做风口上的“专业主义者”
作为国家级先进制造业和现代服务业深度融合试点企业,华米科技有着更大的“野心”,即以“专业主义”和消费者需求作为产品创新开发的出发点,打造全产业链健康生态,为全球用户创造更智能、便捷的生活方式。
上午10点,位于安徽合肥高新区中安创谷的安徽华米信息科技有限公司,楼宇内外一片井然有序的繁忙景象,涌动着一种蓬勃的生机和活力。很少有人知道,这是一家在全球智能硬件公司中少有的年出货量达3000万台的企业。
华米科技成立于2013年,是一家全球领先的智能可穿戴和健康云服务公司。根据国际数据机构IDC的数据显示,早在2017年一季度,华米科技智能可穿戴设备的出货量,已经超过了美国老牌厂商FitbitCONTROL ENGINEERING China版权所有,位居全球第一。
作为国家级先进制造业和现代服务业深度融合试点企业,起步于智能可穿戴设备的华米科技现在有着更大的“野心”,即以“科技连接健康”作为新使命,以“专业主义”和消费者需求为产品创新开发的出发点,通过“芯端云”战略,打造全产业链健康生态,为全球用户创造更智能、便捷的生活方式。
专业就是做到极致
记录步数超过230万亿步、睡眠记录200多亿条,心率记录总时长近3000亿小时、房颤判断准确度达94.76%……这是华米科技智能可穿戴设备为用户提供的最新的全天候健康监测服务数据。
时间拨回到2014年夏天,公司成立仅1年,在价格动辄上千元的智能手环市场,华米科技定价仅79元的智能手环一经推出很快获得消费者的青睐,不到1年时间就卖出超1000万台。价格便宜的同时,公司研发团队并没有让用户的体验打折,计步、来电通知、睡眠闹钟等核心功能一应俱全,续航时间也远超同类产品。
极致的性价比是如何打造的?产品又是如何做到深入人心的?
“要将硬件产品做到极致就必须打造自己的芯片,将软件做到极致就要拥有自己的操作系统,这样才能生产出功能多、性能好、续航长、成本低的极致产品。”在华米科技创始人黄汪看来,公司成立前,研发团队一直专注于智能可穿戴设备领域,已经拥有10多年嵌入式系统研发的技术积累,公司很快迎来爆发式的业绩增长。
芯片的功耗是华米科技研发团队的攻坚要点。经过不懈努力,公司发布了全球首颗智能可穿戴的人工智能芯片“黄山1号”,此后又更新迭代推出性能更加优越的“黄山2号”,整体运算效率提升了38%,整体功耗则下降了50%,让用户不再为续航焦虑。
另外,智能手表早已不是传统的手表,而是一部戴在手腕上的,集定位、通话、记录等多种功能于一体“智能手机”。
为此,研发团队在传感器技术和算法方面下足了功夫。今年9月,该公司推出的第四代GTR和GTS 旗舰新品,搭载了全新一代生物追踪光学传感器,配合升级的心率算法,降低了运动时因手臂晃动造成的信号干扰。
“我们在技术上力争做到更专业,更懂用户的需求,最终打造出超出用户预期的好产品。”黄汪说,公司始终坚持做风口上的“专业主义者”,专注投入的长期主义和追求极致的专业主义成为企业最重要的底色。
人才分布式创新
“华米科技虽然是从合肥开始创业,但一开始我们的着眼点就不仅仅在合肥,而是放眼全球。”黄汪说。
从合肥成长起来的华米科技将总部设在了当地的创业地标之一——中安创谷。然而,企业的1000名员工却遍布在全球5个国家的11个城市。
“核心人才团队的底子和积淀,决定了一家公司能走多远。”黄汪回忆说,公司成立第2年就在硅谷设立了研发机构,成立工艺设计团队,这也为后来公司发展提供了强大的人才储备。现在,公司在北京、深圳、上海、南京等地以及北美和欧洲都设立了研发机构,组建成全球创新中心。
“我们不是把所有人才全部招到合肥,而是要符合产业分布的特点,哪里人才多,就在哪设立研发分支机构。”华米科技公共事务总监张利介绍,人才分布式创新主要围绕产业链布局人才链,吸引全球各地各类产业人才加入华米科技,将分散在企业内部和外部的创新资源有机结合起来。
不仅放眼全球招贤纳士,公司还牵手高校联合培养高层次人才。企业把研发人员送到高校深造,高校也会把“对口”人才送到企业来实践,双方合力把具有前沿性和探索性的成果运用到未来的技术储备上。
值得一提的是,2020年,公司成立人工智能研究院,与钟南山院士团队合作,共同推动智能可穿戴设备在呼吸健康管理方面的应用研究和成果转化。研究院还同中国科学技术大学先进技术研究院展开合作,组建脑机智能联合实验室,探索利用智能可穿戴设备实现癫痫检测、神经调控等多项应用。
一组数据显示,过去3年,华米科技每年用于研发的投入超4亿元,去年更是高达5.15亿元。截至目前,专利申请达1100多项,通过授权的专利650项。
“产品+服务”融合发展
如今,华米科技的智能设备全球累计出货量已超2亿台,产品遍布全球90多个国家和地区,实现了从智能硬件芯片、操作系统,到传感器、健康云服务的核心技术和关键环节的自主可控。
眼下,愈来愈多的行业巨头纷纷拓展智能可穿戴市场。如何在激烈竞争中突出重围占据一席之地?
精准洞察消费者需求成为华米科技的有力武器。记者了解到,该公司品牌部门定期向消费者推送满意度调查问卷,研发人员会对产品进行持续优化改进,力争为消费者带来极致的产品体验。
在调查问卷中,有一个关键问题是:您愿不愿把我们的产品推荐给身边的朋友?这在专业术语上叫作净推荐值(NPS),也可俗称为口碑。“消费者对产品的认可十分重要。如果一件产品做出来之后净推荐值较低,那就要反思这个产品为什么不成功,消费者不满意在哪。”张利说。
此外,随着先进制造业和现代服务业深度融合发展,越来越多的制造业企业正从提供单一产品向提供“产品+服务”乃至“制造融合服务”转变。黄汪表示,华米科技不仅要做智能可穿戴设备提供商,还要成为健康云服务提供商。企业正以“科技连接健康”作为新使命,通过“硬件+数据+服务”的全新模式,深挖大健康产业的市场潜力。
“消费者购买的不仅是我们的产品,还有更多的增值服务。”张利表示,未来,企业继续以推进消费服务重点领域和制造业创新融合为目标,通过智能可穿戴设备开展运动健康等增值服务,满足重点领域消费升级需求,推动智能设备产业创新发展。
薄如蝉翼、光似镜面,厚度仅0.07毫米,超出设备设计极限42%
“蝉翼钢”是如何炼成的
“蝉翼钢”与明信片的结合不仅展示了当今中国钢铁制造业的先进水平,也让企业高水准钢铁制造能力得到淋漓尽致的体现,产品的高品质则来源于企业对每一道生产工序的精益求精、严格管控。
站在首钢京唐钢铁联合有限责任公司镀锡板事业部的厂房库区,看着一卷卷高科技钢材成品“蝉翼钢”整齐码放控制工程网版权所有,等待着装车发货,首钢京唐公司镀锡板事业部副部长莫志英自豪感满满。
莫志英所在的部门负责“蝉翼钢”系列产品研发、生产和质量管控工作。让他更为自豪的是,在党的二十大召开期间,中国邮政发行了“蝉翼钢”明信片《长城颂》,这套明信片采用镂空技术,可以看作是真正的“钢铁长城”,产品一面世就被抢购一空。
鲜为人知的是,这套明信片所用的材料正是由首钢京唐公司生产,这也是中国邮政发行的“北京2022年冬奥会运动图标‘蝉翼钢’明信片”使用过的钢材。“蝉翼钢”与明信片的结合不仅展示了当今中国钢铁制造业的先进水平,也让企业高水准钢铁制造能力得到淋漓尽致的体现。
小小明信片有上千个质量控制点
“蝉翼钢”也被称作“5G钢”,主要为5G基站信号接收器、信号发射滤波器、集成电路板用钢,因厚度薄如蝉翼而得名。
产品的高品质来源于企业对每一道生产工序的精益求精、严格管控。
薄如蝉翼、光似镜面是“蝉翼钢”系列产品的最大特点,也是企业科研攻关的难点。如何攻克这些技术难关,秘密就藏在了轰鸣的生产线之中。
走进“蝉翼钢”生产现场,炼钢、冷轧等一道道工序有条不紊地进行,厚度堪比普通A4纸的钢材源源不断生产出来,最薄的只有0.07毫米。
记者了解到,“蝉翼钢”生产流程包含炼铁、炼钢、热轧、冷轧等四大主流程,包含300多个小工序、上千个质量控制点。
“每次轧制‘蝉翼钢’都是巨大的挑战,从炼钢成分把控到工艺印刷等各个环节,团队都制定了详细的计划,实现全流程管控。”首钢京唐公司镀锡板事业部产品管理室综合主管吴明辉告诉记者。
在生产车间,首钢京唐公司镀锡板事业部镀锡作业区四班作业长段宗灿手捧着《长城颂》明信片,言语间难掩激动之情:“看到自己生产的‘蝉翼钢’‘飞’到了党的二十大代表手里,特别骄傲!”
在谈到“蝉翼钢”生产的电镀工序时,他说:“因为这套明信片采用的是镂空技术,这种印刷技术对于基板的光洁度要求更加严格,几乎不允许有任何瑕疵出现。”
为此,他们通过精准调控轧制力和控制模式,保证了带钢轧制运行的稳定性,还通过调整弯辊力等措施完美化解了轧辊边部的异常接触问题,实现了产品的稳定生产。
高端产品迭代升级
现如今,高强、减薄、高延伸的镀锡产品在各行各业应用广泛。首钢京唐公司积极发挥设备、工艺和技术优势,大力推进极薄规格DR材(二次冷轧材)产品的研发生产。
莫志英表示,“绿色、减薄、高性能是‘蝉翼钢’极薄系列产品的极致追求。”
今年前三季度,企业0.15毫米及以下极薄规格产品的订单量月均占比9.7%,比去年同期上升4.8%。
“历经三年的科研攻关,我们一直在突破极限,把宽幅‘蝉翼钢’的厚度从0.11毫米降到了0.07毫米,超出设备设计极限42%,达到世界先进水平!”莫志英告诉记者。
在这个过程中,整个研发生产团队展现出了敬业、专注、坚持的匠人精神。
首钢京唐公司镀锡板事业部工程师于兴旺说:“‘蝉翼钢’之所以薄,是因为这种钢板对材质密度等属性要求极高,对全流程管控能力要求也极高。”
为了确保钢水的洁净度,技术人员每次都要对钢水全流程氧含量、钢水温度等重点指标进行监督指导。另外,由于带钢太薄,超出了轧机自动调整范围,加之生产过程轧制力大、张力波动大,极易发生断带问题。如何保证轧制过程的稳定可控,也是必须要解决的一道难题。
经过反复研究论证,他们通过对机组张力、烘干温度等一系列参数进行调整,最终解决了带钢跑偏和断带的难题,摸索出一整套极薄规格宽幅带钢的生产工艺,为后续顺利生产打下了基础。
在追求极致的道路上,高端产品的迭代升级不断展现着首钢京唐公司不俗的研发实力和高水准的制造能力,“蝉翼钢”的研发优势正转化成实实在在的制造能力。
“现在‘蝉翼钢’一天可以生产1000多公里,用‘一日千里’来形容一点也不为过。”莫志英说。
不甘心跟跑争领跑
市场是检验产品的唯一标准。
近年来,首钢京唐公司坚持精品战略,以市场为导向,以用户为中心,着力推进产品结构升级、渠道优化、质量改进,加快构建“制造+服务”优势,持续做优做强自己的品牌。
相关数据显示,今年1至10月份,公司开发新产品102项,锌铝镁外板、纯锌外板、酸洗板、镀锌汽车板等多个类型产品实现批量供货;超高强钢强度级别达到1180兆帕,合同兑现率达到95%以上;中厚板9Ni钢、液化石油气船用高强钢等产品成功轧制……
首钢京唐公司技术中心副主任徐海卫说:“‘蝉翼钢’属于低碳钢类超薄极限产品,生产过程中克服了行业上‘钢水纯净度高、酸连轧和双机架轧制薄’的‘三难’问题,这得益于科研人员与生产现场技术人员协同攻关。”
记者了解到,目前,企业产品可生产牌号达到3021个,汽车板、镀锡板等多个主要产品市场竞争力处于行业第一梯队。
“我们正按照‘协同、创新、求真、引领’的工作理念,瞄准‘高效、高品质、绿色、智能’方向,加大高端产品的自主创新。要不甘跟跑争领跑,敢于向国内外一流强企发起挑战。”徐海卫对企业未来发展信心十足。
在他看来,企业不断向高端产品市场进发,不仅仅是巩固自身的竞争地位,抢占市场制高点,更重要的是提升自主创新能力,打造特色品牌。只有经过这样的锤炼和考验,首钢京唐公司才能登上一个新台阶。
屡次刷新吊装重量世界纪录,牢牢掌握关键核心技术话语权
工业重器的“智造”秘诀
针对产业链中的发展难题,徐工集团全力做好技术攻关,加大研发投入,打造自主可控的核心零部件产业,不仅为企业自己的机械装备供应核心零部件,更是为中国装备制造贡献“硬核力量”。
12月8日,在江苏徐州工程机械集团有限公司(“徐工集团”)塔机智能制造基地,十余辆红色重卡满载着黄色塔机结构件,缓缓驶出。到达目的地常泰长江大桥的施工现场后,这些结构件将被组装成一台全球最大塔机,并在300米以上的高空完成一系列最大吊重超过300吨的钢塔吊装作业。
工程机械是国家基础设施建设不可或缺的装备,彰显着中国制造发展的新高度。
近年来,徐工集团凭借一台台自主研制的工业重器,一次次让外界惊艳,引领行业高质量发展。依托领先的技术和过硬的产品质量,徐工集团从全球工程机械制造商排名第11位逐步跻身到第3位,产品远销190多个国家和地区。记者近日走进徐工集团,探访这些工业重器从制造到“智造”的秘诀。
无人化生产,效率加倍
在车间入口除尘后,记者走进徐工集团液压阀智能车间。在这个封闭式恒温车间,举目四望,车间里的机器正有条不紊地运转,现场却看不到多少工作人员。
智能化立体仓库、机加工自动化线、自动导引运输车……一系列前沿的智能制造技术在这里一一实现。徐工液压事业部总经理陈登民介绍,2011年,徐工开始进军高端液压阀领域,随着“高端液压阀智能制造及产业化项目”的落地建成,徐工集团已经实现年产3万件高端液压阀,并逐步成为智能制造的行业标杆。
“以前采用人工上料,劳动强度大,生产效率低。如今通过搬运机器人自动上料,比原来的生产效率提高一倍。”陈登民说。
类似的“智造”场景,在徐工随处可见。
来到徐工传动科技有限公司全自动电控变速箱生产线,几台机器人正忙着将一个个零部件“吃”进生产线。“生产线24小时作业,一天能装配50台电控箱。”操作员袁涛自豪地说,机器作业效率是以前人工操作的3倍,装配精度也大幅提高。
“我们已具备高精度齿轮制造能力、高精度箱体加工能力、热处理加工能力,为推动产品结构转型升级奠定基础。”徐工传动副总经理吕昌告诉记者,近四年,徐工传动先后引进1条数字化热处理工艺产线、9大智能化生产线,制造装备总体数字化率达到95%以上。
“这些液压件、传动件是工程机械核心零部件,以往我国在这些领域基础薄弱,常常受制于人。针对产业链中的发展难题,徐工全力做好技术攻关,加大研发投入,打造自主可控的核心零部件产业,不仅为企业自己的机械装备供应核心零部件,更是为中国装备制造贡献‘硬核力量’。”徐工集团党委书记、董事长杨东升说。
技术赋能,设备“说话”
在徐工集团徐州重型机械有限公司的生产车间,通过5G技术的赋能和大数据的运用,“万物互联”正得以实现。各类物料清单、库存信息在电子屏幕上一览无余,工人们通过远程操控,发布生产指令。
要实现这种远程操控,依靠的正是我国第一个自主研发的工业互联网平台——徐工汉云工业互联网平台。
“有了这个平台,设备可以‘说话’,更加智慧、安全。”站在一块超大电子屏前,徐工汉云技术股份有限公司创始人、CEO张启亮向记者演示起来。他手拿遥控器,点开一张世界地图,上面呈现出很多光点,“每一个光点就代表一台徐工生产的机械设备,设备的各项运行参数在上面一目了然,如果出现故障也会自动提示”。
张启亮说,目前,徐工汉云工业互联网平台已成功赋能装备制造、建筑施工、有色金属、新能源等80多个行业,服务企业超7万家,技术应用惠及全球。
今年5月,巴西矿业巨头淡水河谷公司采购了一批徐工矿山开采机械设备。依托徐工汉云工业互联网平台,这些挖掘机、宽体车等大型工程设备可实现在线调度、远程遥控施工,施工现场实现无人化作业,大幅提升了矿区作业安全性和生产效率。
“这些设备智慧、安全、技术含量高,我们很高兴可以与中国工程机械制造商深度合作。”淡水河谷采购代表马尔科·布拉加说。
自主创新,产品迭代
11月14日,我国自主研制的全球最大吨位全地面起重机——徐工2600吨起重机在山东成功完成陆上最大风力发电机组的安装,实现了起重性能和作业效率的新突破,再次刷新了全地面起重机最高最大吊重世界纪录。
这台起重机吊装的风机,单个机组部件最重可达171吨,相当于100多辆家用汽车加起来的重量。该起重机总设计师李长青表示,徐工围绕千吨级以上全地面起重机持续开展自主研发攻关,目前已成功实现进口替代。
相关数据显示,近五年来,徐工全地面起重机从1200吨、1600吨、1800吨,再到现在的2600吨,屡次刷新最大吨位全地面起重机世界纪录,牢牢掌握关键核心技术话语权。
不仅是起重机,徐工生产的工程机械整机设备、核心零部件等均实现全面迭代升级:新型电控传动箱、大吨位湿式桥、负载敏感多路阀等一批高端零部件实现自主可控;4000吨级“全球第一吊”、700吨级“神州第一挖”、35 吨级“神州第一铲”等一大批产品成为基础设施建设的“国之重器”,多项首台套重大技术装备填补国内技术空白。
“面对复杂多变的形势和疫情考验,中国工程机械产业在危中思变,释放了高质量发展的巨大能量,这背后的源动力就是自主创新。”杨东升表示,自主创新已经嵌入徐工的发展基因,成为企业搏击市场的“通关密码”。
近年来,哪怕面对行业寒冬,承压前行,徐工每年的研发投入占比始终保持5%以上。1999年徐工专利数仅为6件,目前徐工拥有授权专利9600余件,发明专利2300余件,国际专利160余件,5项国家科学技术进步奖,7个制造业单项冠军。
记者了解到,徐工目前汇集了总数达6000多人的研发团队,占集团员工的四分之一。集团高技能人才占比达57.4%,生产一线技能人员占比提升至65.7%。企业持续推动以市场为导向的激励机制,持续强化原始创新、集成创新,已有约200名高级技术专家获得股权激励。
展望未来,杨东升表示,徐工将坚持科技是第一生产力、人才是第一资源、创新是第一动力,加快推进产业高端化、智能化、绿色化,早日建成产品卓越、品牌卓著、创新领先的世界一流现代化企业。
紧盯市场需求搞研发,多次打破国外技术垄断,22年来创造100多个同行业第一
“一专多能”的机器人“智商”有多高
从成立之日起,新松公司便聚焦国家战略和产业发展需求,不断强化自主创新能力建设,努力把核心技术牢牢掌握在自己手里,始终走在追赶世界先进机器人技术的路上。
蛇形臂机器人灵活程度宛如人的手臂;移动机器人随着指令在车间内灵活移动;工业清洁机器人自动清洁粉尘……在辽宁沈阳新松机器人自动化股份有限公司智慧园生产车间,展现在记者眼前的是一个神奇的机器人世界。
机器人被誉为“制造业皇冠顶端的明珠”,其研发、制造、应用是衡量一个国家科技创新和高端制造业水平的重要标志。
从仅有40人的机器人研究所,发展成为规模大、产品线全的机器人上市公司——成立于2000年的新松公司坚持自主研发,多次打破国外技术垄断,用创新铺就智造路,22年来创造了100多个同行业第一,不仅让机器人产品更多能、更智能,也已经成为国内制造业的一张智慧名片。
不断满足现代化生产需要
飞机零部件结构复杂,检测时看不清内部结构;对核电站进行检测、清理掩埋核废料存在巨大危险……长久以来,飞机零部件检测和故障处理、核废料清理可谓世界性难题。
“这些难题必须解决,因为这是特殊行业安全生产的需要,也是对职工生命健康保护的需要。”新松公司特种机器人研究院院长李贺说。
2016年起,新松公司特种机器人研究院开始了蛇形臂机器人的研发工作。
研发团队从零开始,从蛇的灵巧性获取灵感,潜心研发和生产,逐步突破了蛇形臂机器人本体结构、运动控制、路径自主规划等多项关键技术,成功研制出国内第一台蛇形臂机器人,极大提升了机器人的灵活度和适应性。
李贺告诉记者,蛇形臂机器人采用钢丝绳牵引驱动,柔韧性高,空间适应能力强,可以应用在狭小空间和恶劣环境领域。另外,蛇形臂有12个关节,每个关节都能移动,臂长1—3米,在可达范围内都可工作,大幅提升了探测和清除作业效率。
上个月,新松公司的另一王牌机器人产品——星卫来工业清洁机器人在2022全球工业互联网大会刚一亮相,立刻吸引了不少参观者驻足观看。
记者在新松公司的生产车间看到了外观类似滚筒洗衣机的星卫来机器人,虽然看着有些笨拙,但它的强大功能却令人惊叹。
“这款机器人所到之处,粉尘、污水、脏东西立刻不见踪影CONTROL ENGINEERING China版权所有,遇到障碍便可绕过去,还可以与其他机器人协同工作。”新松公司移动机器人研究院副院长吕祥仁说,该款机器人融合了移动机器人控制技术、导航技术、传感技术等多种技术,有效解决了传统工业领域清洁作业面临的劳动强度大、智能化程度低、生产效率低等难题,尤其适合智能化无人工厂、无人仓库使用。
“只要市场有需要、产业有需求,不论多难也要研发出来,力争在洁净工厂装备、智慧物流等方面满足现代化生产的需要。”李贺说。
让机器人更聪明
近年来,随着移动互联网、大数据和人工智能技术的发展,我国制造业不断向自动化、智能化迈进,机器人成为关键角色之一。新松公司紧跟产业转型升级步伐,努力让机器人更聪明、更智能。
新松公司工业机器人技术执行总监孙宝龙指着一排红色机器人说,这些机器人名为火弧机器人,是焊接机器人的最新升级产品,它的最大特点就是“智商”更高,可以“一专多能”。
记者了解到,过去的焊接机器人只是具备焊接功能,而火弧机器人却集多种功能于一身,只要换上不同的工具就能打磨、抛光、喷涂。
“因为有了力觉,干什么活儿它就能使多大劲。”孙宝龙说,火弧机器人应用了更先进的激光扫描传感器、力矩传感器等,使机器人有了力觉和感知能力。因为智能化程度更高,这款机器人受到了广大用户的青睐。
在火弧机器人的不远处,还有几台叉式移动机器人来回穿梭。据该款机器人的研发工程师马驰介绍,以前,叉式机器人在车间运输时www.cechina.cn,要在地面、墙上设置识别标志,叉式移动机器人“看”到标志后才能正常运行。最新研发的叉式移动机器人应用了3D导航技术、末端识别技术等新技术,哪里有需要运送的物品,它自己就能找到。如果需要运送的物品摆放不正,它还会自己调整姿势,照样装运。
“过去是让它干什么它干什么,现在机器人可以思考着干。”马驰说,这款机器人可广泛应用于新能源、仓储物流等环境要求较高又有较大搬运量的领域。
坚持自主创新
生产一台机器人,从安装零件、搬运,到检测、成品入库,只需要一名工程师输入指令,其余全由机器人独立完成……在新松公司,智能化生产场景随处可见,这背后则有一支高素质、跨领域的研发团队做支撑。
新松公司技术执行总监杜振军告诉记者,新松公司研发人员占员工总数的75%以上,这些人才大多是复合型人才,他们通力合作,奋力攻关,一项项技术难关才得以被攻克。目前,公司已拥有工业机器人、移动机器人、特种机器人、协作机器人、医疗服务机器人五大系列百余种产品。
事实上,从成立之日起,新松公司便聚焦国家战略和产业发展需求,不断强化自主创新能力建设,始终走在追赶世界先进机器人技术的路上。
记者了解到,近年来,我国机器人技术水平和产业链完整度持续提升,运动控制、高性能伺服驱动、高精密减速器等关键技术和部件加快突破,核心零部件国产化的趋势逐渐显现。
以新松公司为例,在机器人“大脑”方面,攻克了高实时性智能控制器设计技术,实现了机器人运动自主可控;在机器人“上肢”方面,攻克了高精度轨迹规划与控制、高可靠性设计等技术;在机器人“感官”方面,攻克了基于二维/三维视觉的视觉伺服、碰撞检测与保护等技术,实现了机器人自主作业与人机协作;在机器人协同方面,实现了机器人群体协同……
通过持续深度开发和优化机器人控制技术、核心算法,新松公司正努力把核心技术牢牢掌握在自己手中,成为支撑世界机器人产业发展的一支重要力量。
平均每1.7秒可生产一个电芯,缺陷率仅十亿分之一
“极限制造”点亮“灯塔工厂”
受益于新能源汽车产销两旺的良好态势,动力电池市场需求“水涨船高”。为了应对日益复杂的制造工艺和满足高质量的产品需求,宁德时代提出了“极限制造”理念,在不断突破电池性能极限的同时,积极拥抱智能制造。
走进宁德时代新能源科技股份有限公司湖东工厂涂布车间,繁忙的产线上,搅拌均匀的浆料正以每分钟80米的速度被均匀涂覆在6微米薄如蝉翼的铜箔上。涂布是锂电池生产的核心工序,完成这项操作的,正是该企业自主研发的全球第一台6微米涂布机。
这是宁德时代“极限制造”落地生根的一个生动注脚。作为新能源汽车的“心脏”,动力电池的重要性不言而喻。成立11年来,以智能制造技术为依托,凭借“毫厘必争”的迭代创新和“点滴必较”的质量把控,宁德时代已连续5年蝉联全球动力电池销量冠军,全球每三辆电动车中就有一辆装载其生产的电池,旗下宁德工厂更是被世界经济论坛评选为电池行业首家“灯塔工厂”。
1微米的战役
长久以来,“续航里程”一直是制约电动车发展的最大痛点,宁德时代决定啃下这块“硬骨头”。
过去10年,研发团队持续开展高性能电池技术开发、不断探索化学材料升级,将续航里程从不到200公里提升到超过700公里。
在宁德时代动力电池工程师王升威看来,研发团队还可以在电池包空间利用率上“做文章”:“普通电池包由模组构成,每个模组包含约10个电芯。如果取消模组结构,直接把电芯集成到电池包,同样的空间就可以容纳更多电芯,能量密度能够再提升20%。”
然而,结构的重塑对电芯一致性要求极高。从生产环节看,承载着电芯正负极材料的糊状浆料在自动负压罐中充分混合搅拌后,经涂布工序被均匀涂到铜箔上形成极片,再由高速卷绕机将极片与绝缘膜卷绕在一起形成电芯,其厚度达60毫米。在电池内,每排电芯的数量约20~30个,经测算,只有将平均厚度偏差控制在0.1毫米之内,才能实现直接组装。每个电芯内部有超过100层极片,每层之间允许的厚度差仅有1微米。
王升威团队经过反复测验发现,控制电芯一致性的“通关秘籍”在于浆料:浆料必须流动性能好、黏度稳定、不易发生固体沉降。
他和团队耗时一年反复尝试,最终得到了理想的配方:石墨、黏合剂、导电剂和水的特定比例混合。由此,电池的能量密度提高到220Wh/kg以上,电动汽车的续航里程提升至1000公里以上。
“近十年,动力电池能量密度的增长带来续航里程6~7倍的提升。”宁德时代董事长曾毓群说。
值得一提的是,今年6月,企业发布新产品“麒麟电池”,该电池系统集成度创全球新高,体积利用率突破72%,能量密度可达255Wh/kg,整车续航里程可达1000公里。
“智变”引“质变”
近年来,受益于新能源汽车产销两旺的良好态势,动力电池市场需求“水涨船高”。为了应对日益复杂的制造工艺和满足高质量的产品需求,宁德时代提出了“极限制造”理念,即在不断突破电池性能极限的同时,积极拥抱智能制造www.cechina.cn,打破速度、良品率、劳动生产率和能耗领域的4大“极限”。
“涂布曾经是电芯生产过程中品质管控最难、人工操作最复杂的工艺流程,如今只需一台平板电脑就可以进行实时精准控制。”宁德时代湖东工厂智能工厂负责人冯安民向记者介绍,中央智慧工艺感知控制系统将车间内所有与涂布机相关的设备连接在一起,依托5G技术高带宽、低时延的特性,涂布过程实现了8K高清视频采集,产品一致性大幅提升。
“我们运用人工智能、数字孪生、边缘计算等7大智能制造技术,建立了‘极限制造’体系架构,打造了多平台、多系统深度交互的工业化和信息化深度融合的生态。”冯安民说。
在“极限制造”的加持下,湖东工厂变得越来越“聪明”:增强现实专家系统仿若“千里眼”,技术人员佩戴AR/VR眼镜“身临”生产现场;200多台自动导引运输车“闲庭信步”,有序完成电芯上线、物料循环配送等任务;超高速运动全量视频流AI质量检测“严阵以待”,无延迟采集传输并反馈结果,有效识别微小缺陷……
世界经济论坛在认定宁德工厂为“灯塔工厂”的评语中这样说:宁德时代三年内实现了在生产每个电芯耗时1.7秒的速度下仅有十亿分之一的缺陷率,同时将劳动生产率提高了75%,将每年的能源消耗降低了10%。
纪录正不断被刷新。眼下,企业“四川时代”生产基地通过进一步应用工业物联网、柔性自动化等技术,实现生产线速度17%的提升,于今年10月再度获评“灯塔工厂”。
科技创新步履不停
“随着动力电池迈向TWh(太瓦时)时代,唯有创新可以赢万变。”在曾毓群看来,技术创新能力是宁德时代的核心竞争力,也为企业赢来了客户的广泛认可。
除了破解锂电池的续航痛点,曾毓群表示,针对电池的低温痛点,宁德时代优化了热管理系统,兼顾到加热过程中的无损、安全和高效;针对安全痛点,实现了无热扩散的最高安全要求;在结构创新方面,研发团队突破了单一材料体系性能边界,提出并实现了在单个电池包中布置AB两种不同电芯的设计方案,形成优势互补。
值得一提的是,宁德时代已经构建了以5G为基础的工业互联网架构,通过5G技术与“极限制造”碰撞融合,探索出了22个具有高价值的业务场景,目前已落地9种5G融合应用,朝着5G工厂的目标加速迈进。
强大创新能力的背后,是一支“硬核”的人才队伍。记者了解到,宁德时代在宁德、江苏溧阳、上海、厦门以及德国慕尼黑设立了五大研发中心,研发人员超过1.4万人,其中21C创新实验室已成为全球能源存储转化前沿技术的研发高地。企业还拥有电化学储能技术国家工程研究中心、福建省锂离子电池企业重点实验室、中国合格评定国家认可委员会(CNAS)认证的测试验证中心,设立了“博士后科研工作站”“福建省院士专家工作站”等。
数据显示,2022年前三季度,宁德时代研发投入达106亿元,同比增长130%。拥有及正在申请的国内外专利合计14040项,主导或参与制修订超过80项国内外标准。
如今,宁德时代已拥有世界最全面的电池技术路线布局,以及从技术到产品再到商品的最快转化链条。展望未来,曾毓群说:“新能源的大时代已经到来,我们将以持续领先的产品和服务,支撑引领产业高质量发展,为实现‘双碳’目标和全球电动化贡献更多智慧和力量。”