At a time when few manufacturers were adding new production lines, Southland Tube broke ground on a strategic new mill near downtown Birmingham
www.cechina.cn, AL: its first plant capable of turning thick sheets of steel into 6- to 12-in. wide circular and square tubing used in heavy duty structures and products
控制工程网版权所有, including oil rigs
控制工程网版权所有, bulldozers and rail cars. The new facility, Southland's Mill 5
CONTROL ENGINEERING China版权所有, would enable the firm to expand further into the highly competitive
and lucrative large structural steel tubing market before anyone else in the region, Southland Tube's plant engineer, Steve Barrett, did much of the work himself — from the electrical engineering for the main power distribution to the very detailed and painstaking design of the automation and
Control system that would allow operators to electronically manage, monitor, and maintain the massive production and packaging lines seamlessly. Southland Tube's own design team hand picked the construction contractors, mill manufacturer, production line equipment and machinery.
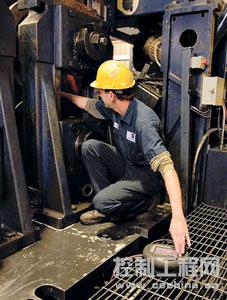
Southland Tube's operators are able to tweak controls on a massive welder witha remote HMI touchscreen.
Mill 5 is by far Southland's largest tube production facility and the most complex integration job Barrett had ever taken on in more than 20 years as an engineer. It's the kind of job most plant managers would hand over to a trusted team of systems integrators. However, this plant engineer—a former systems integrator himself—trusted his instincts and opted to keep the bulk of the project in-house. Barrett ultimately spent more than 3控制工程网版权所有,000 hours in one year designing and managing the project.
Barrett says there was never any doubt when it came time to choose the automation platform. "This is a Siemens plant all the way. I was thoroughly convinced upfront that we needed S