创新支撑战略宏图
近百年来,汽车行业领域鲜有创业成功的公司,而特斯拉的出现,创造了一个新的历史,2003年创立以来,通过不到20年的发展,已经取得了令人瞩目的业绩,2020年7月控制工程网版权所有,特斯拉的市值就超过了传统汽车巨头丰田。仅仅2个月以后,特斯拉的市值就超过了后面9大汽车企业的市值之和。去年十月,特斯拉市值杀进了万亿美元。这个万亿美元俱乐部只有苹果、微软、沙特阿美、谷歌、亚马逊和脸书。虽然当前市值又回到两年前,但特斯拉依然决然向苹果挑战。特斯拉以惊人的创造力,打造了令人眩晕的上升曲线?如此陡峭的成长,是如何形成的?
答案可能是朴实无华,那就是通过创新最终实现制造能力的持续提升。
特斯拉全面的创新,无论是从电动汽车核心的电池、电机、电控的三大技术,到以中央计算模块、左右车身控制模块三大部分组成的域控的电子电气架构,到一体铸造为典型代表的新材料、新工艺技术、以及持续升级的软件系统、远远领先的数据应用,特斯拉一直走在创新的前沿。
除了在相关技术进行突破外,特斯拉在营销模式和制造模式等方面的创新也是可圈可点。更为关键的是,特斯拉开源了电动车的所有专利,构建起了全新的生态体系,特斯拉的核心理念是“新能源车的对手不是同行,而是传统的燃油车。要想打败燃油车,就要尽可能地团结一切力量,要把电动车技术广泛应用,中国的“蔚小理”等为代表的造车新势力,均收益于特斯拉的开源策略,才得到迅猛的发展。
围绕产品,特斯拉在电池、电机、电子电气架构、芯片、软件及自动驾驶技术等方面都有相应的突破,支撑了特斯拉不断推出受市场所追捧的电动汽车。
控制三电
电池技术是特斯拉引以为傲的优势领域之一。专利数据显示,电池系统相关专利占比超60%。特斯拉电池动力系统包括电池单体、电池管理系统(Battery Management System,BMS)、热量管理系统、冷却管理等。
在占据电池动力系统成本70%的电池单体上,特拉斯选择了具有成熟应用的圆柱电芯进行应用,选用圆柱电芯的主要原因在于,借助其成熟的工艺和自动化程度高等特点,可以迅速的实现特斯拉从0到1的过程,同时通过迭代升级,特斯拉从之前的18650,到2170,到现在的最新款的4680,无论在能力密度、续航能力、每千瓦的成本方面均有很大的提升,以最新款的4680为例,通过结构、材料等方面的创新,其能量密度比之前的提升了5倍,续航能力提升了16%,而每千瓦时成本却降低了14%。
当然选择圆柱电芯也带来了一个新的问题,那就是因为数量巨大,而且充放电是一个非线性过程,因此对电池的管理带来了挑战,特斯拉通过自主研发的电池管理系统,很好的解决了这一难题,同时电池管理技术也成为特斯拉最核心技术之一。
在电机技术方面,特斯拉大胆尝试应用了之前传统车企都没有应用的永磁开关磁阻电机。并通过技术革新,如在定子加入少量稀土,并设计了控制算法来平滑扭矩波动,最终提高了电机输出功率,因此Model 3的永磁开关磁阻电机具有体积小、成本低(稀土使用量非常少,而且无需使用铜芯,降低铸造成本)、功率高等优点。相比于Model S/X感应电机83%的能量转化效率,Model 3的能量转化效率提升至89%,即89%的电能可以最终转化为驱动力,这样便进一步降低了电耗,提高了续航里程。
最值得关注的是,特斯拉在电子电气构架上,进行了大刀阔斧的改进。结合电子电气架构从分散到集中的发展趋势,从第一阶段Model S 和 Model X 的功能模块划分(采取的是功能模块划分,分为车身域控制、自动驾驶域控制、中控显示域控制)到第二阶段Model 3的中央计算模块 CCM(Hardware 3.0)和左右车身控制模块的域控模式,大大降低了ECU(电子控制单元)的数量,从传统汽车的几十上百个ECU,减少到三个,节点变少的同时线束也缩短了,可以高效的提升组装的效率。
CCM是整车最高决策者,接管所有辅助驾驶相关的传感器,例如摄像头、毫米波雷达等,并管理各核心控制器。前车身控制器,由于位置靠前,主要负责执行自动驾驶模块、座舱模块、压缩机及车前灯等;右车身控制器,负责气囊控制、12个超声波泊车雷达、热管理、扭矩控制等;左车身控制器,负责内部灯光、后电机控制、充电模块等。
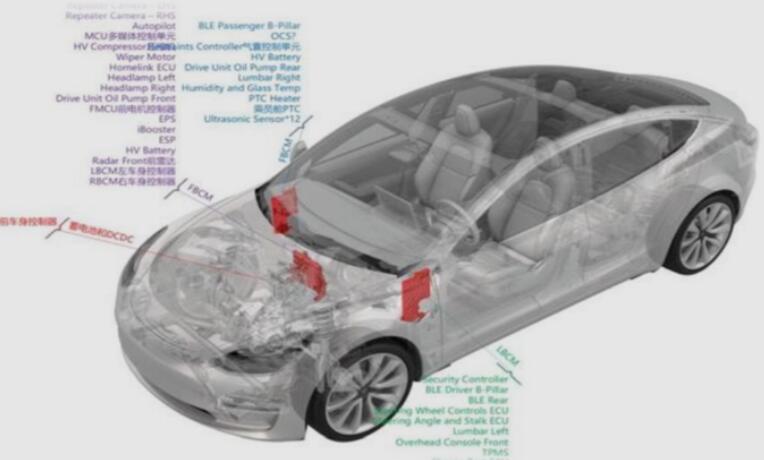
芯片主驱、软件定义
在全新的电子电气构架下,对于模块的功能和软件定义提出了更高的要求,尤其是对算力的指数级增长。因此特斯拉将创新延伸到了上游芯片领域,2015年特斯拉就开始招兵买马自研芯片,2019年4月推出了自主研发的车载芯片,其算力到达了144TOPS,远超于当时竞争对手的21TOPS,可以从容的支撑L3级智能驾驶的算力需求,而且功耗很低,特斯拉也成为拥有自主芯片的车企,在目前车企普遍面临芯片断供的情况下,游鱼得水,应付自如。
有了好的构架、算力的支撑,自然就需要软件系统的支撑。特斯拉通过“软硬件解耦、算力集中化”的思路,真正地实现硬件标准化和软件开发重复利用,既实现供应商可替代,也可以大大缩短软件迭代周期。同时特斯拉通过OTA(空中下载技术),通过软件系统升级持续地改进车辆功能,至2020年底,特斯拉已经累计进行59次OTA升级,除了解决应用程序、地图等功能的升级外,特斯拉更是通过软件升级,可以将Model 3的续航能力提升5%;百公里加速度从4.4秒降到3.9秒。同时特斯拉也实现了将硬件,也就是车和软件分拆销售的模式。
有了硬件和软件的加持,特斯拉在自动驾驶领域,也打破的传统车企持续升级的路线,通过技术的快速迭代,实现从L1到L5的发展,为其无人驾驶出租车进行了铺垫。通过数据开放等方式引入IT巨头,借力谷歌/百度等IT巨头,实现深度学习、OTA升级等方式不断优化自动驾驶可靠性和安全性,实现产品快速迭代升级。截止2021年1月1日,特斯拉有效收集了51.3亿公里的行驶数据,远超其他竞争对手几个数量级。
惊人的超级工厂
相比于特斯拉在电动化、智能化等方面的创新,特斯拉的生产制造能力一直被低估。特斯拉不仅能研发设计出最好的电动汽车,而且还能最高效、最低成本地生产电动汽车。2021年,特斯拉汽车业务毛利率高达30.9%,远高于传统车企。以特斯拉Modle 3为例,单车的利润超过了6万元,与国内很多电动车车企每卖出一辆就亏好几万形成了鲜明的对比。
特斯拉在产品实现领域的升级可以从工厂布局的持续优化、自动化&智能化不断磨合、新材料&新工艺&新技术持续创新、核心零部件自主化、其他零部件本地化等方面进行体现。
从特斯拉的产能布局来看,目前拥有的美国加州工厂、我国的上海工厂、德国柏林工厂、德州四大超级工厂已经投产,未来还会有更多的超级工厂。
从四个工厂的布局来看,在不断的迭代,加州工厂由于是收购通用之前的总装基地,因此布局上还是相对分散的,到了中国的上海工厂,按照冲压、焊装、涂装以及总装四大工艺进行合理布局,到了柏林和德州工厂更是实现了动力电池和汽车生产的有效衔接。
包括大众CEO也不得不感慨:特斯拉今天可以用7000个工人实现年产50万辆车的效率,而大众需要15000人。究其原因,是工厂的整体设计非常合理。对传统车企来说,很多分立的产房和车间都被特斯拉有机的整合在一起了。
埃隆·马斯克将这些超级工厂的设计称之为“同一屋顶下”的设计,即按照工序,实现门对门、口对口的设计,省去了一个车间造好零件、装车运往下个车间的过程,不仅仅提升了效率,而且节约了成本。
同时特斯拉超级工厂在设计时,不仅仅考虑平面的布局,更为关注空间立体布局,使得工厂更为紧凑和高效。更为关键的是这些设计理念,特斯拉通过digital twin来进行实现,也就是在实体工厂建造之前,在计算机中实现了合理的布局,而且通过多度的仿真,使得布局更加合理。
在自动化方面的投入,特斯拉是不予余力的,这些都源于埃隆·马斯克有一个梦想,就是让机器制造机器。当然埃隆·马斯克也在不断反思。通过早期加州工厂超前自动化所带来的教训,特斯拉曾尝试用大量机械臂代替人工完成组装,将传统汽车行业总装阶段的自动化率由8-15%一度跃升至50%,但由于设备调试经验不足,机器人效率低下,产线过度自动化使得产能投放受限,因此不得不降低组装环节自动化率,拆除一些效率低下的机器人,如在拧紧座椅的固定螺栓、连接座椅供电线、为座椅套皮套等方面,雇佣工人来代替。埃隆·马斯克如今更强调的是人与自动化的协同。为了稳步提升其自动化水平,这些年来特斯拉不断收购了与自动相关的很多公司,以提升其在自动化的能力。
即使在汽车最常规的四大车间,特斯拉也采用X光扫描的视角,深入骨头逐一审视每一种工艺的合理性。
对于冲压车间:特斯拉的冲压车间采用了中控室一体控制的模式。全封闭的冲压环境,能够有效减少外界异物粘贴到凹模与凸模,从而降低冲压件诸如点蚀、凹坑等局部缺陷出现的机率。目前,上海工厂冲压车间的终端收料环节仍采用人工搬运方式,但在柏林工厂已经采用机械手进行搬运。焊装生产线采用了由左、右、上三台机器人同时进行工作,相比传统的左右两台机器人,三台机器手臂的协调难度更大,但是生产效率进一步提高。焊装车间的自动化率达到94%,主焊部分的自动化率更是达到100%。
每个车间都有自动化强化的痕迹。在检校车间:机器人会从1900个位置扫描Model 3的车身组装线,确保其符合设计规范,把误差保持在0.15毫米范围内。同时特斯拉通过大量引入AGV,实现物流的自动化配送,从而改变了传统汽车生产线依靠板链的固定流水线生产方式,实现了柔性生产。
特斯拉在制程工艺环节也在不断优化。传统汽车厂商生产一部汽车,需要130至200个步骤,而Model 3只需40余步骤(尽管也有电动汽车比传统燃油车的零部件要少得多的因素)。
要支撑特斯拉的超级工厂,仅有自动化是远远不够的,还需要庞大的信息系统做为支撑。
在管理信息化方面,特斯拉早期应用了SAP的系统,但在2012年决定放弃SAP而采用自研。刚开始基于低代码开发平台Mendix作为开发工具进行开发,仅用了四个月,就完成了系统的开发和上线,不久后特斯拉也实现了低代码平台的的自主化。特斯拉的信息系统叫Warp Drive(“Warp”),经过多年迭代,Warp成为全公司遵循统一的软件开发管理准则,Warp集中、集成和优化整个公司的供应链、产品计划、库存、销售订单管理、资产、财务等业务流程;用户在车机系统上的求助及报修功能等,也都直接连接到Warp系统中。
在生产执行方面,特斯拉自主研发了生产制造控制系统(MOS),具备人机交互、智能识别及追溯功能等,深入支持世界顶级的制造工艺。除了MOS系统,在上海超级工厂,高可靠性的工业网络覆盖自动化生产线的各个角落,保证产品生产过程的标准化,充分利用大数据系统回溯每台车、每个零部件的生产数据。
在质量管理方面,通过数据采集系统实现了从细节到整体的全方位数据收集,不仅达到全尺寸监控和管理,还实现了整车工厂与全供应链零件尺寸检测数据的实时采集和大数据分析,对尺寸偏差进行预判。
数字化技术、信息化系统与自动化的结合与融合,支撑了超级工厂的高效运行。
绽放的材料和工艺
特斯拉在材料和工艺的持续创新,是非常值得关注,最无人熟知的是一体铸造技术。目前已经在上海工厂、柏林工厂等多个工厂进行批量的应用。通过这样大胆的尝试,借助一体化铸造技术,使得零部件从传统的70多个变成2个,传统的50台压铸机和200台加工中心的工作由一台大型压铸机完成。除了效率的显著提升,成本也降低了70%左右,而且质量和减重方面都有不俗的表现。同样值得期待的是,目前特斯拉正在尝试电池+车身一体化工艺,将电池直接内嵌在汽车结构中。这将进一步减轻车辆的整体重量,减少中间工序。
伴随着汽车智能化水平的不断提升,汽车电子应用越来越广泛,传统汽车上用到的线缆也越来越多控制工程网版权所有,而线束的生产一直是汽车生产中较为复杂的,一方面是线缆本身的生产组织;另一方面预装好的线缆安装到车体上,这些都需要大量的人工来进行操作,而且很容易出错。特斯拉通过底层的电子电气构架的创新,使得其线束从Model S的3公里,缩短到Model 3的1.5公里,到Model Y的100米。较好的解决了其效率、质量等难题控制工程网版权所有,同时成本、轻量化等方面得到大幅的缩减,在此基础上,特斯拉还在材料上进行优化,用铝导线代替传统的铜导线,进一步降低了制造成本。
在电池制备方面,特斯拉2019年收购了 Maxwell,因此获得了其超级电容、干电极、负极补锂等相关技术。全新的4680电池就采用了干电极工艺,通过无溶剂方式进行加工。不仅仅提高了电池的能量密度,而且效率提升7倍。这将使得每千瓦时的成本,降低56%。
未来特斯拉在新材料&新工艺&新技术领域的创新,有一项应用非常值得期待。皮卡产品Cybertruck的车身颜色不是采用传统的喷涂工艺,而是借助冷轧钢回火后不同温度域的颜色变化来实现其不同颜色。这真是一个惊人的想法,传统汽车的喷涂工艺将会彻底颠覆。对于一个汽车厂而言,喷涂车间不仅建设成本高,运维成本也很高,最最重要的是环保压力非常大。当颜色不再由油漆实现,而是金属本色的呈现,世界会是什么颜色?
此外,特斯拉还不遗余力寻找每一个工艺优化的可能。特斯拉通过设计优化,实现不同电路板的左右拼接生产,电机铝合金外壳的应用、前悬控制臂及前后转向节通过结构优化,实现强量化等。
有了这些独到的制造优势,特斯拉就总会表现得与众不同。就在原材料涨涨涨,电动汽车集体涨价之后,特斯拉今日突然宣布再一次降价,让整个汽车市场都为之一颤。
2021年,特斯拉汽车业务的毛利率高达30.9%,远高于传统车企。以特斯拉Model 为例,单车的利润超过了6万元。降价任性的特斯拉,自有它节省成本的方式。在供应链管理方面,特斯拉秉承“核心零部件自主化、其他零部件本地化”的思路,除了动力总成中的 BMSCONTROL ENGINEERING China版权所有,自动驾驶系统(软件与芯片),电机驱动模块和制动系统由特斯拉自己生产,其他零部件大部分为外购,并且强调就近本土化供应。
重新定义客户价值
围绕客户价值,特斯拉在营销模式上也彻底打碎传统代理销售模式,建立了直销体系。与传统汽车营销借助4S店的分销模式所不同www.cechina.cn,特斯拉采用的是自营门店的销售模式。
在传播方面,特斯拉是很少进行广告营销的公司,而是借助埃隆·马斯克的巨大影响力、名人效益和创新事件进行网络裂变式传播,例如2018年2月,SpaceX成功的将一台特斯拉汽车送上太空,引起了巨大的轰动,同时特斯拉也较早将汽车展示开到了大型商场。
相比传统整车5-8年车型换代周期,特斯拉可以通过OTA升级不断提升产品性能,且通过对部分高端功能OTA升级进行收费,创造更多收入增长点。传统主机厂基本上只能通过销售前端产品获得收入和盈利,特斯拉创新了商业模式,软硬一体化搭建“终端+软件+服务”全产业链服务。虽然目前软件销售在其整体收入占比还不是很高,但是正在稳步的提升。
汽车目前真正的使用时间其实仅为其整个生命周期的5%(95%的时间汽车只是被放在车库或者停车场),特斯拉发扬了“共享出行”的理念,通过Robotaxi的方式增加车辆的使用效率。特斯拉车主可以将自己的车加入到 Tesla Network以此来共享自己的特斯拉,通过Robotaxi APP让汽车与车友相匹配,从而让车在被自己闲置时也能保持使用状态。将目前作为支出项的汽车摇身一变成为资产。
这种模式看上去只是一个商业模式,其实很难直接复制。它的核心是规模优势和算法壁垒,形成较大规模之后才会形成较好的网络效应。算法的积累也会给出行销量带来提高,匹配最有效率的订单。在自动驾驶完全实现之前,特斯拉的共享出行服务实际上是为了让车主赚取出行费用的同时,使更多的消费者可以体验特斯拉汽车, 加大其对品牌的宣传力度。
小记:回归制造
特斯拉作为行业趋势引领者,在电动车产业链尚未成型的年代,完全靠着出色且大胆的技术集成思路,从传统制造出发,进行了耳目一新的变革,从而迎来了时代的尖叫。
这很容易让人意识到,那些已经烂熟于心的制造方式,依然有着惊人的改善空间。制造创新依然是一门方兴未艾的新风口。