A proportional-integral-derivative (PID)
Controller operating in a feedback loop can be very effective at driving a measured process variable towards a desired setpoint, but only if the controller is adjusted or tuned to accommodate the behavior of the controlled process. For a PID controller using the ISA standard form of the PID formula, tuning is a matter of selecting appropriate values for the tuning parametersP
CONTROL ENGINEERING China版权所有, TI
www.cechina.cn, and TD shown in the formul
a to the right.
The PID formula determines the control effort (a.k.a. the conroller output) CO(t) from the process variable PV(t) and the error e(t) between the process variable and the setpoint. The conroller can be made more or less aggressive by modifying the three tuning parameters - the controller gain P
CONTROL ENGINEERING China版权所有, the integral time TI and the derivative time TD.
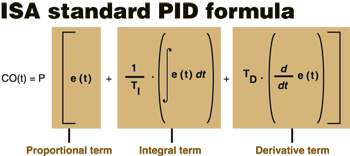
Like all PID formulas, the ISA standard form computes the error between the process variable and setpoint as well as the integral and derivative of that error. It then weights the proportional term by a factor of P
CONTROL ENGINEERING China版权所有, the integral term by a factor of P/TI
www.cechina.cn, and the derivative term by a factor of P·TD where P is the controller gain
www.cechina.cn, TI is the integral time, and TD is the derivative time.
Tuning the loop—or more correctly, tuning the controller—requires adjusting those weights so that the controller can eliminate errors quickly without making matters worse. If the controlled process happens to be relatively sluggish, the controller can be tuned to take immediate and dramatic action whenever a random disturbance changes the process variable or an operator changes the setpoint. A relatively large value for P and a small value for TI would be appropriate in this case.
Conversely
控制工程网版权所有, if the process happens