提高质量效益www.cechina.cn,推行优质制造,是实现中国制造突破性变革的必然选择。优质制造作为支撑质量变革、增加优质供给的创新模式,是实现我国制造业高质量发展的重要依托,是提升国家核心竞争力的关键内容。为此,开展优质制造技术体系与发展策略研究,对于建设制造强国、质量强国具有积极意义。
中国工程院林忠钦院士科研团队在中国工程院院刊《中国工程科学》2022年第2期发表《我国优质制造技术体系建设研究》。文章在深入剖析我国制造质量发展痛点的基础上,基于供给端、需求端、政府监管、质量基础设施“四位一体”框架,分析了优质制造提升的关键问题,提炼了优质制造的内涵与特征,构建了“设计 – 生产 – 运维”全流程的优质制造技术架构。文章研究表明,我国制造质量仍存在质量效益有待进一步提高、制造品牌国际影响力不强、产业链质量升级面临困境等痛点问题。所构建的优质制造技术体系由质量技术基础、质量共性技术、全生命周期质量管控技术、资源要素等模块组成。建议加强优质制造标准体系建设,加快推动产业链质量升级,创新质量发展体制机制,提升质量资源要素供给能力,加速新技术赋能优质制造,夯实质量技术基础。
来源:中国工程院院刊
作者:林忠钦,奚立峰,夏唐斌,赵亦希,潘尔顺,李艳婷
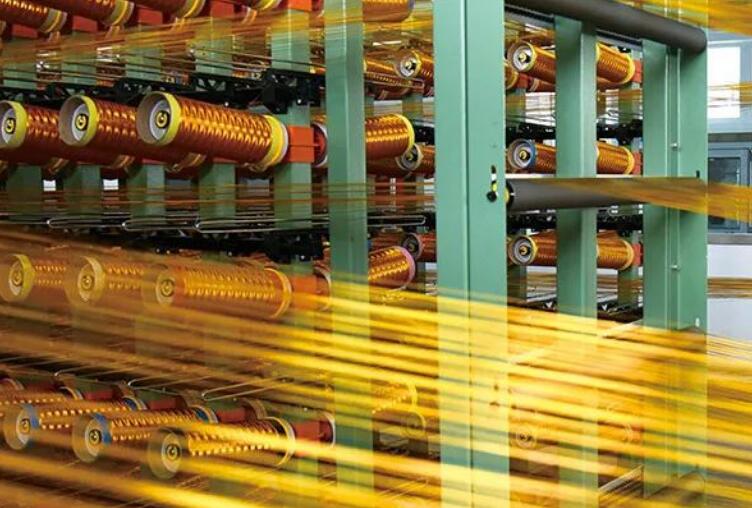
一、前言
当前www.cechina.cn,全球制造业分工格局经历着深刻调整,我国制造业发展的外部环境和内部条件正在发生重大变化。从外部环境看,新一轮科技革命和产业变革深入发展,全球经济发展风险日益增多,新型冠状病毒肺炎疫情影响广泛且深远,科技“脱钩”风险加剧,发达国家制造业回流趋势明显,经济全球化遭遇逆流;从内部条件看,传统制造优势逐渐丧失,境外疫情持续扩大使产业链、供应链受到冲击,不确定性与风险加大。加快形成以国内大循环为主体、国内国际双循环相互促进的新发展格局,正是国家在这样背景下作出的重要部署。我国经济发展整体向好,但制造业投资增速处于低位徘徊,提升制造业核心竞争力依然面临挑战。
面对经济新常态的发展要求,优质制造成为提升国家核心竞争力的关键内容。在优质制造概念提出后,学者围绕该主题开展了一系列研究。深入剖析中国制造质量的热点问题,提出了夯实质量基础设施、发挥品牌制胜效应等优质制造重点任务建议;实施全员质量素质提升工程、重塑“工匠精神”等结论,指明了优质制造领域的人才保障路径;提出的优质制造生态概念,从系统工程的视角丰富了优质制造框架;聚焦医疗器械、机床等具体行业,针对优质制造瓶颈环节提出了发展策略。然而,现阶段研究在优质制造关键技术方面尚未形成共识,也未提出具体的发展路径;亟需以技术性需求为研究切入点,探索形成优质制造提升的发展策略。
本文深入剖析我国制造质量发展痛点,基于供给端、需求端、政府监管、质量基础设施有“四位一体”框架,分析优质制造提升的关键问题,提炼优质制造的内涵与特征;从优质制造的质量技术基础、质量共性技术、全生命周期质量管控技术、资源要素等维度出发,构建涵盖“设计 – 生产 – 运维” 全流程的优质制造技术体系,以期为优质制造的理论和应用研究提供基础参考。
二、我国制造质量的痛点问题与提升关键点
(一)我国制造质量发展的痛点问题
1. 质量效益有待进一步提高
纵观改革开放 40 余年的发展历程,我国制造业规模已居世界第一,但质量效益远低于发达国家。对比入选《财富》世界 500 强的制造企业平均利润率可见,我国制造企业的平均利润率仅在 3% 左右,与美国的 9.1% 相比差距较大,与德国的 4.3% 亦有一定差距(见图 1)。“中国制造”长期在价值链中低端徘徊的现象并未彻底改变,质量效益亟待进一步提升。
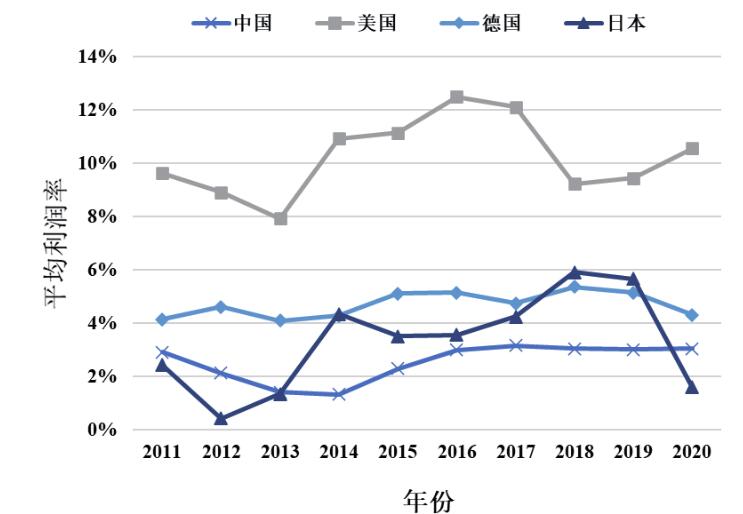
图1 4个国家入选财富 500 强制造企业的平均利润率情况
2. 制造品牌的国际影响力不强
近年来,我国品牌建设不断加强,制造企业的品牌国际影响力有所提升。从世界品牌实验室发布的世界品牌500强制造企业的影响力值可见(见图2),我国制造企业的品牌影响力与德国、日本、法国的差距有所缩小,但与美国仍有较大差距。制造品牌的国际影响力受到多重因素影响,如产品可靠性、一致性、稳定性等质量特性指标不尽如人意,技术能力不足导致的质量问题是制约中国品牌影响力的最重要因素。亟需通过提升技术能力夯实制造品牌影响力,改善“中国制造”的国际形象。
3. 产业链质量升级面临困境
着眼产业链全局,我国产业链质量升级主要面临三方面困境。
一是产业链质量供给能力不足。据工业和信息化部 2018 年对全国 30 多家大型企业 130 多种关键基础材料的调研结果,32% 的关键材料仍为空白,52% 的关键材料依赖进口,产业链供需不匹配的矛盾越发突出。
二是产业链质量提升动力不足。优质不优价、“劣币驱逐良币”、低价竞争的现象仍然存在,部分产业链存在利润分配失衡现象。
三是产业链质量协同力度不足。以半导体产业为例,我国大部分企业集中在产业链低端环节,在中高端环节的高质量稳定批量生产中存在技术不足,尚未建立有效的产业链协作模式;根据美国半导体行业协会 2021 年研究报告,在 2020 年全球半导体产业链总营收中,中国大陆企业仅占 5%,与相应消费占比不相称。
(二)优质制造提升的关键点
实现优质制造是系统性协调发展的过程,从系统角度建立基于供给端、需求端、政府监管、质量基础设施“四位一体”的逻辑框架,分析优质制造提升的关键问题(见图 3)。
在供给端,供给体系尚未满足产业需求,产品质量的整体可靠性需进一步提高。我国制造质量效益与发达国家存在差距,中高端质量的自主品牌建设缺乏;日益变化的产业发展和全球贸易环境,在关键技术方面的投入和创新不足,制约了我国制造企业开展优质制造的能力和意愿。我国制造核心技术仍受制于人,许多新技术、新产品停留于实验室研究阶段,在产业化应用时面临可靠性、一致性、稳定性问题。
在需求端,政府采购中的低价中标制度与优质优价理念相违背,消费者对优质产品及其价格的接受程度与购买意愿不高。我国消费群体两极分化现象严重,主流群体因购买能力受限而倾向低价产品;消费者高度关注产品质量及安全,但对国内产品质量认可度较低,使得国内购买意愿欠缺而更热衷于海外消费。
在政府监管方面,价格政策和质量监管机制尚不完善,相关低价政策未能兼顾质量和价格,造成 “低质低价”的市场局面。政府对相关产品的分级定价收购政策没有从市场对质量特征的需求出发,不能有效传递质量信息。产品质量监管力量不足,缺乏长效监管机制;企业质量违约成本低,因违约处罚力度偏弱致使督促约束作用不明显。我国制造业从业人员的整体素质、技术与技能水平不强,培养体系尚不完备;人才培养模式单一,人才培养总量短缺,制造人才发展受限。
在质量基础设施方面CONTROL ENGINEERING China版权所有,先进有效的标准体系还未形成,新兴产业的基础设施发展滞后。计量检测设备依赖进口,高端检验检测能力供给严重不足;在战略性新兴产业和生命科学、人工智能(AI)等高技术领域,存在“检不了、检不出、检不准”等问题。产品优质分级的认证制度缺失,标准制定过程对优等品的界定不明确、不统一,缺乏与优等品对应的认证,不利于提供品牌保障。
三、优质制造的内涵与特征
(一)优质制造的内涵
“优质制造”是以国家质量基础设施为核心基础,以优质资源要素为保障,面向产品全生命周期,综合应用大数据、智能制造、工艺优化等共性关键技术,考虑“互联网 +”、共享经济、服务制造等新模式和新业态的影响,精准把握客户需求,全面提升产品质量和效益,将产品从“良”提升至“优” 的一种新型制造模式。
优质制造的核心是“精准、精益、精确、精细”。
①需求精准感知,应用大数据、智能预测等技术,感知顾客需求的动态变化并传输到系统精益优化的输入端;
②系统精益优化CONTROL ENGINEERING China版权所有,将需求落实转化至产品开发设计、工艺优化、生产系统规划、服务系统优化等环节,以产品增值为导向进行决策优化;
③过程精确控制,面向制造全过程开展数据分析,借助物联网技术并结合工程知识,对全过程进行精确控制,保证过程的稳健性;
④要素精细管理,分析全生命周期中全要素对产品质量的作用机理,集成并应用质量管理方法来实现全要素的协同与融合。
(二)优质制造的特征
优质制造的主要特征如图 4 所示。
一是国际竞争力,“优质制造”好不好,关键在于质量效益好不好、有没有形成产品竞争优势。
二是品牌影响力,品牌依托于产品的质量,质量是品牌的保障,好的品牌影响力意味着高溢价能力。
三是可持续的创新能力,代表了优质制造的发展潜力,这是评价优质制造水平的一个重要指标。
四是卓越的产品和服务,优质的制造全过程最终体现为优质的产品和服务。
四、优质制造的技术体系架构
优质制造技术架构由质量技术基础、质量共性技术、全生命周期质量管控技术、资源要素等模块组成(见图 5)。具体来说,质量技术基础和质量共性技术是“地基”:前者包括标准技术、计量技术、检验检测技术和认证认可技术,后者包括大数据分析技术、统计分析技术、信息管理技术、工程知识分析技术、AI 技术。三大“支柱”涵盖产品全生命周期质量管控技术,包括优质设计、优质生产、优质运维。资源要素涉及加工与试验装备、工业软件、核心基础零部件(元器件)、关键基础材料等产业基础,最终服务于高端装备及消费品的优质制造提升。
(一)优质制造质量技术基础
以标准、计量、检验检测、认证认可为要素的质量技术基础,是公认的提升质量竞争能力的重要技术手段,也是新时期优质制造技术发展的基石。目前,质量技术基础正逐步向智能化、国际化、集成化发展。
在制造业工业化和信息化高度融合的背景下,质量技术基础不断升级,赋能优质制造。以新一代智能化技术发展为基础,推动共性技术标准研制,实现高水平标准供给;开发智能计量测试技术,为提高计量精确性、促进制造工艺优化提供有效工具;创新智能在线检测技术,提高故障探知效率,确保制造过程的高可靠性。
对标国际先进水平,加强前沿质量技术基础研究,引领产业国际化、高端化发展。研制产业前沿技术国际标准,推动颠覆性技术创新,加速原创性成果转化;突破高准确度、高稳定性量子计量基准,在航空发动机等高精尖制造领域获得应用示范;发展对接国际的检验检测与认证认可技术,支持突破国际贸易壁垒,提高产品竞争力。
针对全产业链提质需求,加强质量技术基础的要素融合。集成融合是质量技术基础发挥优质制造效能的关键举措。以计量、标准、检验检测、认证认可技术能力提升为基础,建设质量技术基础信息化数据库和集成服务平台,形成解决制造业重大需求的合力。在产业链的上、中、下游各环节,以质量技术基础的融合来实现服务优质制造的协同,为全产业链质量升级提供全面支撑。
(二)优质制造质量共性技术
优质制造技术既体现在大数据分析、统计分析、信息管理、工程知识分析、AI 的技术研发和工业赋能,又系统性地综合上述技术成果,通过质量共性技术融合来实现“设计 – 生产 – 运维”全过程的优质制造技术升级。
创新大数据分析技术和统计分析技术,推动工业大数据的深度挖掘与分析。针对制造系统信号源多、特征复杂的特点,开发多源异构数据测量采集系统。发展海量复杂数据治理技术,综合完整性、规范性、一致性、准确性、唯一性、关联性,进行多维度数据质量评价,贯穿数据的计划、获取、存储、共享、维护、应用、消亡阶段进行质量监控与管理。面向高频、多维、海量的质量数据库,研发高效并行的大数据分析工具,通过多源异构数据与工程的融合、迁移和互补,形成标准化的统计分析及评价流程。
综合应用信息管理、工程知识分析、AI 等技术实现对工业信息和知识的管理及利用。针对现代制造业工业化和信息化高度融合的特点,发展覆盖研发、生产、管理、营销、物流、服务等全流程的信息系统与工业云平台;以实时反馈的信息流为要素,形成全流程信息链,建立信息资源库及工程知识库,消除信息孤岛和知识壁垒。为突破质量问题溯源性差、专家经验通用性差的瓶颈,应用知识库构建技术开发质量管理工程知识库,运用文本分析和字符编码技术对大规模、碎片化知识进行挖掘和融合。依托传感器、大数据、机器学习等技术的快速发展,在用户精准画像分析、制造工艺决策优化、运维过程健康状态监测及维护决策优化等方面深入应用 AI 技术。
(三)优质设计
用户多元需求获取技术指融合定性的用户反馈和定量的市场分析,结合 KANO 模型等工具系统收集、分析和提炼用户需求。开发智能网联爬虫技术,采集互联网反馈的海量数据,研发大数据用户画像技术,结合多元数据分析手段挖掘用户的潜在需求。工业设计作为连接供需双方的载体表达,精准感知特定需求,高效完整地形成用户个性化产品需求。以保证产品质量为出发点,构建由用户需求驱动的“质量屋”,连接用户多元需求与产品性能属性,实现用户定制化的产品设计。
高可靠稳健优化技术指面向产品越来越高的可靠性需求和系统稳健性要求,综合考虑产品的功能、质量、成本等因素,融入新的优化方法,通过推理寻优形成完善的高可靠稳健优化技术理论体系。构建设计、知识联合驱动的产品模型,结合数字仿真技术进行实时评估与改进,主动获取并集成仿真过程中的知识,利用稳健设计和智能优化算法自动修正产品设计参数,提高产品的可靠度和抗干扰能力。
面向全生命周期的设计指将产品全生命周期思想引入工业设计,使产品的设计阶段与制造阶段、装配阶段、使用阶段、回收重用形成闭环融合。开展面向制造工艺的设计,构建整合产品结构、零部件结构、工艺文件等的工业设计知识库,高效形成具有良好可制造性的设计方案。研发基于产品模型的智能设计匹配技术,支持设计、工艺、制造、检验信息等与产品模型的自匹配。面向制造工艺,构建装配过程的数字化模型,通过模拟仿真发现装配问题,及时改进并优化装配设计。面向使用运维,建立包含服务能力、维修资源、部件重用信息在内的运维设计知识库,结合 AI 分析方法将可维修性与可重用性整合到到产品设计,提高产品可靠性。
(四)优质生产
考虑现代制造技术的精密化、极端化、集成化、智能化、数字化等特征,综合应用光学、电子、传感器、图像、制造、计算机等技术,研发基于新原理、新方法、新工艺的科学测量仪器,开发精密检测、在线检测、数字化检测等技术,满足高精度数控机床、大型运载火箭等装备对超高精度、大尺寸结构的测量要求。
针对船舶、航天等重点行业产品工艺过程繁复、精度要求严格、偏差传递复杂等特征,发展工程知识与工业数据双驱动的制造工艺优化技术。集成生产全过程工艺参数的多源制造工艺数据和质量特征测量数据,揭示偏差传递机理;通过质量数据分析与工艺偏差诊断,提升生产控制能力,保障生产过程精度。搭建生产过程工程知识与工业数据融合驱动的优质生产软件系统,开展基于 AI 技术的工序参数优化和工艺精度提升,开发自进化、自迭代的工艺知识推理和优化技术。
研发面向多工序复杂制造过程的预测性过程自动控制技术。基于产品在线测量、误差传递、误差预测、误差源诊断方法,进行制造过程的多尺度建模与分析,形成标准化的制造过程质量参数统计分析流程。突破“材料 – 设计 – 制造 – 性能”一体化的协同关键技术,形成贯穿制造过程全流程的质量信息链,开发具有预测诊断、实时反馈调节功能的生产过程自动控制技术,实现复杂制造过程的质量数据自监控、质量偏差自诊断、质量补偿自控制。
(五)优质运维
开发融合物联网与数字孪生的状态监测技术。结合智能传感器技术、信息融合技术,研发多源数据协同、功能互补的设备产品状态监测技术,对设备使用过程中的各类状态进行智能感知、分析和利用。融合远程监测、云边协同、边缘计算、数字孪生等技术手段,开发虚实映射的物联网数字化管控系统,实现大规模分布式设备状态的在线、实时、精准监测管理,保障设备在服役过程中的高性能与高可靠运行。
发展智能故障诊断决策技术。设备产品朝着自动化、智能化、数字化方向发展,运行状况呈现变负载、变转速、非平稳等复杂特性,应用各种感知技术,开发具有专家系统和智能化功能的故障诊断系统。对设备技术状况进行智能检测和评估,实时诊断故障发生的部位和原因,指导运维人员及时排除故障。推动 AI 与故障诊断技术融合发展,不断提高诊断系统智能化程度,实现故障知识、诊断推理的自学习与自进化。
研发运行状态预测预警技术。针对设备状态监测数据多元低质、高维海量、结构复杂等特点,突破全寿命、全系统、多维监测数据融合难点,采用统计概率、信号处理、机器学习、统计学习等技术构建模型算法,形成兼顾预测准确性、时效性及鲁棒性的智能预测建模技术,实现健康趋势预测、失效停机预知、状态劣化预警,全面保障设备健康安全,提升复杂产品的运维效率与能力。
(六)资源要素
优质制造技术的资源要素包括加工与试验装备、工业软件、核心关键零部件(元器件)、关键基础材料等产业基础,是制造业实现优质制造和质量提升的重要支撑。加强资源要素供给,能为高端数控机床与机器人、航空航天装备、先进轨道交通装备、节能与新能源汽车、家用电器等高端装备及消费品行业的质量保障“保驾护航”。
在加工与试验装备方面,突破高端核心加工装备的国产化瓶颈,建立国产加工装备与工艺集成验证平台,形成国产装备工艺适应性、精度保持性、可靠性综合验证与工艺大数据管理能力,对于加速高端装备研制,构建高质量、高效率、低成本的自主技术体系至关重要。
在工业软件方面,研发具有自主知识产权的工程设计类软件、生产管理类软件、监控运维类软件,支持优质制造全流程提升。工业软件技术突破将支持解决设计、生产、运维环节的“卡脖子”问题,提升优质设计效率、优质生产水平、优质运维能力。
在核心基础零部件(元器件)与关键基础材料等产业基础方面,突破高端机床数控系统、智能装备传感器等瓶颈环节,掌握产业链核心技术和竞争力。例如,荷兰阿斯麦尔公司在光刻机领域的领先地位离不开高超的磨镜工艺和超高的机械精度,而高性能基础材料短板制约着国产射频芯片的性能提升。
五、推进优质制造的对策建议
(一)加强优质制造标准体系建设
加快组织制定 / 修订包括国家标准、行业标准、团体标准等在内的优质制造标准体系,在质量基础设施、质量共性技术、面向优质的设计、制造工艺与服务等方面逐步构建较为完善且有国际水平的标准,形成有利于推动产业链优化、有助于质量效益提升的优质制造标准体系。面向重点产业制定优质制造技术路线图,为相关行业质量升级提供路径参照。建立优质制造评价标准,设立国家优质制造企业奖励措施,制定优质制造企业认定管理办法,经认定的国家优质制造企业可参照“高新技术型企业” 享受所得税税收减免政策。将优质制造企业与增信挂钩,在融资贷款等方面为优质制造企业提供相应的优惠政策。
(二)加快推动产业链质量升级
以事关国计民生的重大装备及热点消费品等为重点,开展优质制造专项行动,提供配套政策和保证措施,优化产业链质量并创新资源配置,筑牢产业链质量基础设施。重点解决产业链关键产品的可靠性、稳定性、一致性等共性问题,通过产业链质量升级来尽快迈向价值链高端。建立有效的资源共享、产业协作、合作经营的协同模式,全面梳理制约质量升级的体制性障碍和技术瓶颈,充分考虑产业链上、下游的特色和差异,实施精准化协同推进。建设一批优质制造试点示范企业,树立优质制造标杆,发挥“链主”企业的优势与影响力,带动产业链整体提升。
(三)创新质量发展体制机制
健全优质优价的市场机制,在政府采购、招投标活动中纳入有关标准技术条件和质量安全要求;鼓励采购优质产品,将“优质优价”理念应用到生产、加工、流通、销售环节,促进产业链条稳固运行。建立合理的全社会收入分配机制,降低行业薪酬结构的差异度,增强制造业竞争力,吸引优质人才资源,激发技术创新活力。构建公平竞争的市场环境,强化政府的宏观质量管理职能,形成高质量的工作机制,通过数字赋能营造规则统一、公开透明的监管环境;全面提升市场监管效能,支持企业创新提升效率和质量。
(四)提升质量资源要素供给能力
加快培养高端质量和品牌人才,持续推进“互联网 +”质量教育,推动实施首席质量官制度,健全开放包容、科学规范、运行高效的多层次质量教育培训体系。提升高端装备资源的供给能力,加强以企业为主体的协同创新,着力解决零部件和系统的质量及可靠性问题;积极支持国产化功能部件的配套应用,逐步突破高端智能测量装备和传感元器件的国外技术垄断,实现从基础件到成套的计量检验检测仪器设备的产业提升。加快工业软件国产化进程,提升国产工业软件的规模和质量,建立国产工业软件竞争优势,形成“产用”合作生态。加大原材料、零部件、元器件的基础理论研究,从产品研发、工艺能力、质量基础设施能力支撑等多方面提升创新研究水平,在提升自身产业整体质量的同时,对下游相关产业质量改善形成重要支撑。
(五)加速新技术赋能优质制造
通过政策引导、市场牵引,加大基础性、颠覆性核心技术研究及投入力度,在物联网、大数据、 AI、云计算等智能科学新技术方向上不断深化,推动信息手段、制造技术、数据科学在优质制造中的深度融合,赋能优质设计、优质制造、优质运维全流程。整合“产学研用”资源优势,实施优质制造大数据战略;针对工业大数据感知采集、加工处理、传输存储、决策分析等各环节,优化工程统计手段、智能分析方法、质量回溯机制,建立优质制造质量动态评价系统。培育优质制造协同创新中心,支持各类企业、高校、科研机构成立优质制造技术研发平台,推动科技攻关项目落地实施;开展优质制造试点项目示范与推广,凸显标杆企业的行业技术创新引领作用。
(六)夯实质量技术基础
完善标准、计量、检验检测、认证认可等优质制造质量技术基础协同服务产业链的流程与机制,建立全链条、全方位、全过程的质量技术基础服务体系,实现以质量基础为核心,标准协调、计量协同、检验检测协调、认证认可协同的产业链质量协同格局。加快建立重点行业全产业链标准图谱,丰富产业基础标准和强制性标准;加强区域产业链计量测试体系建设,实现计量从单台检测到立体支撑产业链的发展;合理整合检验检测机构的优势资源,注重产业链的检验检测能力建设控制工程网版权所有,形成服务产业链的检验检测网络。建立以政府扶持为引导、企业投入为主体、多元社会资金参与的质量技术基础投入机制,提升资源配置效率,发展优质制造创新技术和示范产品。