计算机数控(CNC)技术的起源,可以追溯到1950年代,但现在该技术仍然与机械密切相关。现代CNC的功能不断增加,为需要这种控制水平的行业提供更广泛的工具集。不同类型刀具的发展进步,以及更快的控制硬件和软件,使工程师可以在更短的时间内完成更精确的切割。CNC带来的收益包括:更大的产量、更高的精度、更低的废品率和更少的精整加工。
随着越来越多刀具和多轴伺服系统高性能选项的出现,CNC的应用推动着软件平台持续改进。对等离子切割机、喷水切割机和激光切割机以及铣刨机和刀片等更复杂应用的需求,将传统的CNC软件推向了极限,从而使控制工程师不得不寻求更灵活的选择。
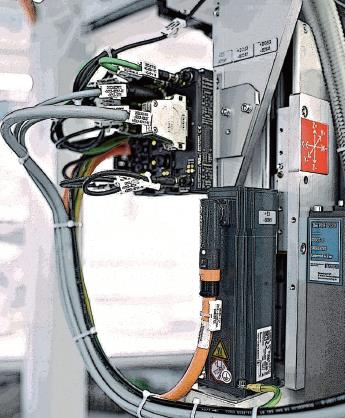
运动设计软件使集成电动机、驱动器和组件变得更加容易。图片来源:倍福
同一平台集成仿真和CAD
基于PC的控制平台控制工程网版权所有,在同一平台上集成了CNC、运动控制和可编程逻辑控制器(PLC)。在很大程度上,这得益于多功能工业PC(IPC)更高的处理能力,它通过消除以前所需的单独硬件设备而有助于提高CNC的性能和精度CONTROL ENGINEERING China版权所有,减少了过去用于相互通信的多个设备,从而使处理周期得以缩短。
如今,基于PC的控制平台控制工程网版权所有,还允许用户在同一工程环境中,轻松集成仿真和计算机辅助设计(CAD)软件。仿真软件程序可以直接与PC控制软件连接,以合并现有的CAD和CNC模型www.cechina.cn,从而加快机器设计速度。它还可以帮助您以经济高效的方式加快原型零件的开发。机器设计可以适应零件原型的变化,这在以前是不可能的。
系统集成的运动设计软件,可以通过扩展工具范围来推动这种主动型机器设计,从而更轻松地确定所需的电机和驱动设备,并将它们与机器中的所有机械组件精确匹配。
将切削缺陷可视化
即使是设计最佳的机器,也必须根据调试所观测到的实际情况进行改进和优化。这些条件(尤其是对于CNC应用而言)可能会因行业、应用和材料类型而异。在切割应用中,用户会观察到锯片偏斜,可以需要根据不同速度和材料对系统进行调整。这就需要可以从高级传感器读取数据的实时软件。
这个过程被描述为通过前馈和监视实时传感器来“欺骗”轴。它使工程师能够解决或应对刀片偏斜,以提高切割性能。创建有效的算法来“欺骗”轴,可以消除挠度并增加产量www.cechina.cn,而不会牺牲精度。通过最大限度地减少原材料浪费和产品报废,提高了整体效率。
无论应用程序类型如何,具备高级功能的CNC都可以利用3D CAD模型将切削缺陷可视化,因此工程师可以在软件中对其进行校正。配置CNC库的基于PC的控制软件,可以运行插值来比较轴,并基于样条控制和最终零件的精确尺寸来计算最佳矢量。有了这些信息控制工程网版权所有,仿真软件就可以根据从轴的观测轨迹及其定义的速度所得出的数据洞察力,来确定最佳的零件切削路径。通过CNC设计的仿真,可以增强使用熟悉工件材料、新材料或原型材料的操作,这样可以确保在部署和调试计算机时获得更大的成功。(作者:Matt Prellwitz)