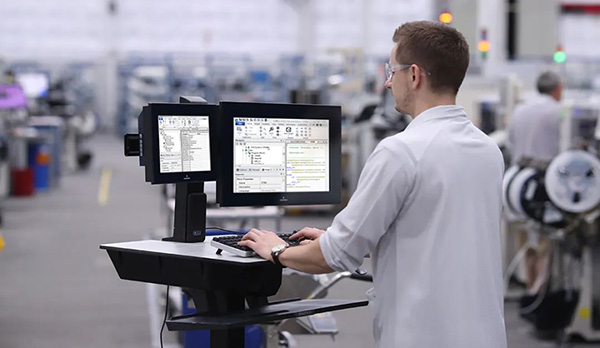
大多数工业自动化应用控制工程网版权所有,都要求控制设备和相关的输入输出(I/O)元件,具有较高的可靠性和可用性。从1968 年推出的第一台离散可编程逻辑控制器(PLC)到现在,PLC 已被广泛应用于制造业生产线的控制。虽然通常使用一组PLC 来精确执行I/O控制,但每个PLC 都需要通信端口和控制器单元,这样系统规模就比较大而且价格高昂。一旦部署完成,升级成本也很高。
在商业(COTS)基础设施上的虚拟化可编程逻辑控制器(vPLC),可以取代大量单独的控制器“机箱”及其电子设备。这就是边缘计算,信息技术(IT)的云基础设施就位于车间机器附近。这样就可以满足极低延迟和短控制周期的严格要求(本文假设边缘计算基础设施位于工厂内部)。
通过将边缘节点上的大量vPLC 相互连接,有助于运营效率的提高。尽管vPLC应用的不是太多,但随着边缘计算的出现,这种架构可能会变得越来越重要。在数据中心,在功能强大的服务器上虚拟化数据库和应用程序一直使用最先进的技术。
虚拟化是将逻辑功能(软件)与物理设备分离,并在商业硬件上运行的能力。虚拟化可以降低成本,提高灵活性和可扩展性,并提高IT 的可靠性和性能。在过去的十年中,很多供应商开始在虚拟化的环境中支持其监控与数据采集(SCADA)和分布式控制系统(DCS)平台,从而在运营技术(OT)环境中实现更多的虚拟化。
最近我们看到,在需要将性能提高到超出其当前控制器能力的情况下,其实已经有越来越多的DCS 供应商开始部署虚拟化控制器CPU,以帮助用户降低控制器成本。这些虚拟化DCS 控制器可以运行在商用IT 硬件上,如Windows 或Linux 服务器。
基于边缘的集成式架构
可以想象以下场景:从车间移除分散的PLC,将其控制功能以vPLC 的形式托管在边缘数据中心,并具有适当的计算能力以及与自动化系统的网络连接的功能。服务器已经可以同时处理数百个vPLC,但配置虚拟化和共享网络和存储资源的标准IT 服务器www.cechina.cn,无法充分满足OT 行业对可靠性和实时性能的要求。为此,需要能够运行实时工作负载的工业边缘服务器。只有I/O 仍然保持在机器、传感器、执行器和驱动器的所在地。
与基于单个PLC 的分散式体系结构相比,集成式体系结构在没有功能变化的情况下,显著降低了资本和运营支出,这主要是因为可以将大量的虚拟化PLC 托管在一台服务器上。
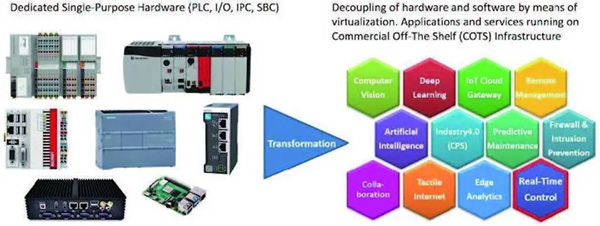
图 1: 制造业正在采用边缘计算来实现 IT/OT 融合。
vPLC 和传统PLC 之间的明显区别在于灵活性和可扩展性。由于实现了控制功能的虚拟化,并运行在边缘数据中心,虚拟控制器之间的交互变得更加简单。虚拟控制器之间的通信,可以通过单个服务器内的功能调用来实现,与物理上分离的PLC 之间的传统通信相比,这提高了可靠性和可扩展性。它有助于生产线的升级和重新设计。在数据中心运行的虚拟控制功能,就像生产线的“数字孪生”,有助于模拟和预测物理对象的行为。
从边缘数据中心访问现场数据的可能性,意味着可以实时执行控制和数据分析,这是诊断、维护、优化和对自动化系统变更实现智能响应的理想选择。
大数据分析不是在边缘服务器上的控件上运行,而是与同一边缘服务器上的控件“并行”运行。因此,现代人工智能(AI)和机器学习算法,可以在不干扰现有控制过程的情况下应用于此。由于将控制功能托管在同一边缘基础设施上,因此也可以在此实现从数据分析到控制的反馈回路,从而开启新的优化选项。
实施虚拟化的4 个挑战
那为什么这种架构尚未被广泛采用?相关调查发现了4 个主要的问题:
01 现有的架构经过了试验和测试:
成本优势、灵活性和优化很好,但收益并不匹配。“切勿触碰运行中的系统”,除非资本和运营支出有收益显著。
02 服务协议和责任:
工厂和运营商从供应商或系统集成商处购买了“封闭式”的解决方案。这些方案通常有封闭的接口,因此机器无法适应不同的控制架构。如果机器未按预期工作,供应商必须修复它。
03 技术风险:
集成服务器平台的可靠性和确定性不够可靠,无法将关键控制功能托付给它。由于网络原因控制工程网版权所有,边缘数据中心中控制器的响应时间也可能不可靠。
04 组织障碍:
要实施此类集成平台,控制专家需要新技能。公司内的人才储备通常与集成架构不相匹配。
在边缘端进行控制虚拟化的优势必须针对每个应用进行判断。作为工业4.0 战略的一部分,边缘计算基础设施对于那些对灵活的生产过程和反应性过程变化有很高要求的应用是物有所值的。技术风险相当具有挑战性,但最近的一些进展表明,在这方面已经有新的突破:
● 实时操作系统和虚拟机监控程序解决方案,已经为当前多核CPU 提供了可靠的资源分区机制CONTROL ENGINEERING China版权所有,如CPU内核和缓存,因此可以实现与“裸机”一样的实时性能,而不是虚拟化和相关的实时波动。内核越多,可以同时独立运行的实时应用程序也就越多。
● 由硬件支持的、本地以太网接口的网络虚拟化,使多个应用能够相互独立地使用同一服务器上的网络资源,并且可以实时在网络中获得所需的带宽。时间敏感网络(TSN)和确定性IP网络,在网络中提供了独立传输来自不同应用程序的实时数据的机制,并且不受以太网网络延迟的干扰。
● 对于各种现场总线协议,如Ethercat 和Profinet,已经提供了通过TSN 定义“通道”的规范。这使得现场I/O 能够通过一个网络与边缘数据中心中的VPLC通信,就像它们通过现场总线直接连接一样。
● 在应用和管理方面,提供独立于制造商的接口已经成为一种趋势。OPC 基金会运动工作组的当前规范工作旨在确保基于 OPC UA 发布/ 订阅的控制和运动控制设备(驱动器、I/O)之间独立于供应商的互操作性。基于OPC UA 和TSN 的制造商独立互操作性的类似标准已被一些工业联盟和协会(例如Euromap和OPAF)采用。独立于制造商的管理接口也可以更好地发挥作用。

图 2:一个假设的自动化平台的潜在架构。
有了这些机制、技术和标准,就可以实现集成的、基于边缘的架构,就像在各种测试平台和演示中所展示的那样。
在编程和实时运行性能方面,控制模型没有任何变化:即使生成的控制应用实现了虚拟化PLC,并且仅通过现场总线接口与现场通信,IEC 61131 编程模型也可以原封不动地使用。此外,一些项目已经按照IEC/EN 61499 分布式控制的要求扩展集成架构。
来自组织方面的挑战也不容忽视。用于承载控制的边缘平台的配置、调试和维护,与PLC 的编程和运行是不同的任务。因此,与以前一样,控制应用的生命周期仍然是这些应用专家所擅长的领域CONTROL ENGINEERING China版权所有,而IT 部门则负责边缘服务器及在其上运行的托管基础设施的安装和维护。
根据自动化行业的要求,确保健壮性和确定性的基本接口,必须包含在经认证的边缘计算平台产品中,因为这种能力通常既不是控制专家擅长的,也不是IT部门擅长的。但这不会改变基本模型中的任何内容。
在自动化领域,基于边缘的集成式控制架构并非是最先进的。目前的架构是很成熟的,其中大多数控制器在其应用中作为硬件PLC 实现。但是,如果需要更大的灵活性,那么将边缘计算架构中的虚拟化控件,与边缘节点和边缘数据中心集成的方法和技术,可以带来更多的好处。
要实现完全的PLC 虚拟化,还面临很多挑战。例如,PLC 确定性与其它传统云服务(如办公应用程序)的不确定性、以性能为中心的本质之间存在根本区别。如果没有一个或多个供应商参与此技术转移,则不可能实现完全的PLC 虚拟化。
尽管在工业控制中使用虚拟化PLC 可以为集成最新ICT 技术提供机会,但在制造业领域的采用率还有待提高。我们建议在绿地项目部署时可以采用虚拟化PLC。为了获得最大收益,它们应该与生产线上的执行器和传感器集成,并使带有虚拟化PLC 的控制器成为智能工厂支持子系统的一部分。(作者:David Lou, Industry IoT Consortium)
关键概念:
■ 越来越多的DCS 供应商开始部署虚拟化控制器CPU,以帮助用户降低控制器成本。
■ 从边缘数据中心访问现场数据的可能性,意味着可以实时执行控制和数据分析。
思考一下:
是什么阻碍了您公司在工业控制中使用虚拟化PLC ?